Epoxy is an impressive material that creates an effective protective layer on top of rough concrete flooring. It is extremely durable and can withstand the weight of heavy vehicles. The smooth surface created by epoxy in garages and parking spaces reduces damage from vehicle tires. It can also be infused with vinyl flakes that improve traction.
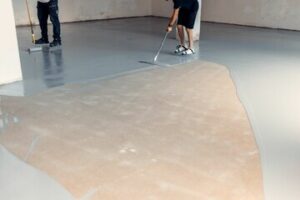
Epoxy Coating Waco TX are strong and durable. They are often used in manufacturing plants and warehouses to protect floors from heavy equipment, chemicals, and other debris that can cause damage. They also resist scratches, dents, and other forms of wear and tear. They also resist moisture, making them a good choice for areas that are exposed to water and other liquids. However, these coatings can still crack and chip over time. This can be a problem if you want your floor to last for years to come.
One way to make your epoxy coating more durable is by adding nanofiller. Graphene, for example, can be used to increase the strength and durability of epoxy. It can also help improve the anti-corrosive properties of an epoxy coating.
An amino-functionalized GO-reinforced epoxy coating exhibited improved corrosion resistance in Q235 steel. The fGO was prepared using the standard toluene synthesis, and was dispersed in THF followed by mixing with the epoxy resin and curing agent. The samples were coated on steel substrates by a bar coater and cured at a gradient temperature. The coating with 1 wt% of fGO showed the best corrosion protection with impedance values of more than 108 O cm2 after 28 days of immersion.
Adding fGO to an epoxy-based coating can be beneficial because it can fill pores and voids in the coating, improving its barrier effect against corrosion. In addition, fGO can enhance the mechanical performance of an epoxy coating by increasing its tensile strength and adhesion to metal substrates. Lastly, it can reduce the occurrence of cathodic delamination by increasing the coating/metal interface area.
A cyanate ester (CE) modified epoxy reinforced with fGO demonstrated improved corrosion resistance in Q235 carbon steel. A fGO suspension in THF/DMF was mixed with CE/epoxy, talcum powder, and glass flake in an acetone solvent. After abrasion and cleaning with acetone, the steel plate was coated with the mixture by a bar coater and cured in a gradient temperature range. The fGO-reinforced sample showed better corrosion protection, with a lower corrosion current density and more positive corrosion potential.
Easy to Clean
While epoxy floor coatings are resistant to many substances that could damage them, they aren’t indestructible. Because of this, it is important to keep them clean as soon as they are soiled. Failure to do this will result in dirt and grime settling into the epoxy and scuffing it up, and this can lead to a loss of shine and gloss.
Cleaning your floors is relatively easy with an appropriate cleaner and a mop or broom. It’s recommended that you do not use a cleaning product that contains citrus or vinegar because these products will degloss your epoxy floor and make it harder to clean. Instead, a dilute solution of ammonia or Simple Green works best for removing spills that have an oily texture. Make sure that you rinse the cleaning agent thoroughly after using it on your epoxy floors.
If your facility is subject to heavy traffic and frequent vehicle movement, you’ll want an epoxy floor that’s easy to clean. It’s also recommended that you keep a neutralizing agent handy, as some chemicals can cause the flooring to lose its initial gloss.
While a one-part floor coating might be suitable for interior surfaces that receive little traffic and are unlikely to encounter moisture, a garage floor or carport slab would serve better with a genuine two-part epoxy composed of 100 percent solids. Water-based two-part epoxy options are available, which are simpler to apply but offer more durability than one-part epoxies.
Epoxy coatings can come in a wide range of colors and textures to suit the style of your space. There are even options that incorporate colored flakes to create unique designs. Once you’ve decided on the color, you can choose from different finishes, including high-gloss and low-gloss.
While you’ll want to consider your budget, it’s important to understand that the cost of an epoxy floor coating is usually less expensive than a carpet or tile. Aside from the cost of the material, you’ll save on labor and installation costs. This makes it an attractive option for businesses that need to minimize their expenses.
Shock Resistant
If you need a durable coating for surfaces that might experience impacts, epoxy is a great option. Its density and depth help it resist shocks, so recreational gear or cars won’t damage your garage floor or concrete countertops. It’s also resistant to moisture, making it ideal for bathrooms and kitchen floors. You can even use it for pool decks and other outdoor applications that need a slip-resistant surface.
Epoxy is a type of polymer resin that can be used in adhesives, coatings, and composite materials. There are a variety of classes of epoxies, including cycloaliphatic and aliphatic. Cycloaliphatic epoxies have a ring-like structure, which makes them more rigid than aliphatic counterparts and better suited for situations where chemical resistance is important. These types of epoxies can withstand high temperatures and offer good mechanical strength and electrical insulation.
A more reliable alternative to cycloaliphatic epoxies are aliphatic epoxies, which have a straight or branched set of carbon chains in their makeup. They’re less rigid than cycloaliphatic epoxies, and they offer excellent UV stability and chemical resistance. These epoxies are often found in marine, automotive, and food applications.
Adding a nanofiller to an epoxy coating can enhance its anti-corrosion properties. For example, a fGO/LM/epoxy sample with 1 wt% of Popd and 0.5 wt% GNP added demonstrated superior corrosion resistance compared to the unmodified epoxy after 300 h immersion in saline solution (108 O cm2), with low polarization and impedance values, and no signs of delamination [52].
Phosphorus-containing epoxies are another type that can withstand extreme heat. These epoxies are usually made with a bisphenol F diglycidyl ether copolymer that’s cured with fatty acid or tetraethylenepentamine. Depending on the grade of the phosphorus, these epoxies can withstand temperatures up to 200 degrees Fahrenheit.
In addition to being heat-resistant, epoxy can withstand a lot of abuse and still look beautiful. It won’t peel or chip, and it will stand up to harsh chemicals like gasoline and brake fluids. In fact, it’s ideal for garage floors because it will keep those harsh chemicals from damaging your car and other equipment in your garage.
Chemical Resistant
Chemical resistance is one of the most important properties that epoxy coatings can offer their substrates. The key to this property is the fact that polymer coatings are inherently impermeable to the chemicals of their surrounding environments, which prevents the transfer of these chemical species to the underlying substrates. However, the chemical resistance of a particular thermoset epoxy system depends on a variety of factors, including its structural composition, crosslinking density, and degree of cure. Molecular modeling and analytical techniques like differential scanning calorimetry, Raman spectroscopy, and dynamic mechanical analysis can shed light on these factors.
The chemical resistance of an epoxy is also impacted by its temperature behavior, as many chemical attacks happen at elevated temperatures. For example, hot oil attacks are common in commercial kitchens, and epoxy coatings that can withstand this kind of exposure are needed to protect flooring from damage. For this reason, many manufacturers develop products with excellent thermal stability and high chemical resistance that can withstand elevated temperature environments.
One such product is Master Bond EP21AR, a two component epoxy resin that can be used for coating, bonding, or sealing applications. This epoxy is formulated with exceptional acid resistant properties, and can withstand prolonged immersion in sulfuric acid and hydrochloric acid for over a year. This unique property makes EP21AR ideal for projects that require exceptional chemical resistance and longevity.
A variety of factors can impact the chemical resistance of an epoxy, but the most significant is its structure. In general, a phenolic novolac epoxy will have greater chemical resistance than a glycidyl epoxy, as it has a more cross-linked structure. For this reason, phenolic novolac epoxy is often used for projects that require a high degree of chemical resistance.
Another way to increase the chemical resistance of an epoxy is by adding a grafting agent. For instance, amino-functionalized fGO (fused Graphene Oxide) has been successfully used for enhancing the anti-corrosive properties of epoxy-based coatings. In a recent study, fGO was functionalized with APTES and added to an epoxy resin/polyamide curing agent mixture. After a toluene bath, the fGO/epoxy/polyamide film was exposed to mild steel and tested for corrosion resistance by EIS.